Introduction
The purpose of this section is to provide the Design Engineer and Buyer with all the information they need when considering the use of thread rolled worms.
All of the design information necessary to take full advantage of the tremendous productivity and performance benefits of the thread rolling process over traditional thread production techniques can be found below. Information on basic material selection, design of thread lead and diameters, the relationship of thread depth and number of starts, the design of thread crest and root features and suggestions about overall part configuration to facilitate thread rolling, will help the design engineer avoid common pitfalls.
The end of this section contains a table of popular worm sizes with specifications and full scale thread profiles shown (see Table 37).
Advantages of Rolled Worms
Traditional threading techniques for worms are metal removal or chip producing processes. Thread rolling, on the other hand, is a cold forging or chip-less process. A hardened cylindrical threading die rotates and presses into a blank workpiece, impressing the die’s thread shape into it. The process is similar to rotating a cylinder of modeling clay between clenched fists.
Advantages of thread rolling are material savings, improved surface finish, better fatigue and ultimate strength, and above all economy of manufacture. Savings of 75% of threading time are common when thread rolling replaces hobbing, milling, and die head threading. Even greater savings result when rolling replaces thread grinding and single point threading. Also, rolled parts are more efficient, and run cooler and quieter than cut-thread parts because of their superior surface finish.
Material Selection
During thread rolling, the yield strength of the work piece is exceeded by the roll die pressure forcing material to cold flow into the shape of the die. Many materials cold form well, and only a few cautions should be observed. Materials with very high yield strengths and those that do not cold form well are poor candidates for rolling. In general, materials harder than HRC 35 and those with elongations less than 12% lack the ductility necessary for rolling. Materials harder than HRC 35 can be rolled in some cases, but die life is so short that the die cost/ productivity trade-off must be studied carefully.
In some cases, materials as hard as HRC 50 have been rolled even though the overall cost was actually higher than that of thread grinding. Most of these applications are related to aerospace or nuclear applications where increased fatigue resistance justifies the cost premium.
Some materials that seem to be ductile and soft enough still cannot be rolled because of their extraordinary work hardening properties. These are typically exotic stainless steels or temperature-resistant alloys on which cold forging data are limited. Cast materials such as gray iron, bushing bronze, and die cast zinc alloys are soft enough, but they lack the necessary ductility and should be avoided.
Materials that machine well usually do not cold form well and vice versa. Additives that promote machinability, such as lead and sulfur, cause the material to separate rather than flow during rolling. Leaded steels and steels with more than 0.15% sulfur content should be avoided for worms and power screws although they are sometimes used for fasteners.
Lead and Major Diameter
Thread lead and major diameter are usually dictated by load, speed, and environmental and physical requirements. In many cases, the screw or worm must be self-locking, which further restricts the choice of lead. To test for self-locking, the value of back-drive efficiency, Eb, must determined. If Eb is negative, the thread is self-locking. If not, the lead must be reduced until a negative value is obtained. This is done by setting the expression for Eb (see the Useful Engineering Formulas section) equal to zero and solving for critical lead angle. Then, a design lead slightly smaller is selected to provide a factor of safety.
Flank Angle
Flank angle is critical to good rolling efficiency and is perhaps the single most important feature of any worm design. Threads with 0° to 10° flank angles are almost impossible to roll because the work piece material tends to shear rather than flow. Although some rolling is done with 7° to 10° flank angles, the practical minimum is 14 1/2°. This is the standard flank angle for Acme threads, and compares favorably with 15° ISO Trapezoidal threads.
Forms with 14 1/2° flanks are easily rolled for lead angles up to 10°. However, as lead angle increases above 15° (typically done by increasing the number of starts), flank angles should be increased to provide clearance and strength in the roll die.
In general, the higher the flank angle, the easier the material flow. Large flank angles keep die pressure low, make part tolerances easier to maintain, and eliminate production headaches such as premature die failure.
Flank angles below 14 1/2° are usually specified for two flawed reasons. The first is that low flank angles result in higher efficiency. While theoretically true, the increase is always minimal. For example, a 5° lead angle on a square thread (flank angle of zero) has a theoretical efficiency of 36% compared to 33% for a 30° flank angle only about 3% difference. Frequently these small differences are nullified by the poor thread finish and sloppy part fit-ups, caused by greater variance in all part features. Both of these are caused by forcing material into difficult shapes. Higher theoretical efficiency, therefore, is rarely a valid reason for specifying a flank angle below 14 1/2°. The second reason that low flank angles are specified is that high angles, over 30°, result in a force component transverse to the thread axis. These are called separation forces for worms and worm gears, and dilation forces for power screws and nuts. Because the influence of these forces on performance can be hazardous, they must be carefully studied. Bearings on the worm shaft can be overloaded and fail early, while nuts on power screws can wear excessively, dilate, and break.
Frequently, a compromise must be struck to provide a high enough flank angle that is easily rolled and yet is not so high as to create excessive transverse forces.
Table 35
ARow | BMaterial Group | CBest for Rolling | DGood for Rolling and Machining | EAvoid |
---|---|---|---|---|
Carbon Steels | 1018 | 1117 | 11L17 | |
Carbon Steels | 1045 | 1118 | 11L41 | |
Carbon Steels | 1050 | 1137 | 1144 | |
Carbon Steels | 1060 | 1141 | 11L44 | |
Carbon Steels | 1151 | 12L14 | ||
Carbon Steels | 1213 | |||
Carbon Steels | 1215 | |||
Alloy Steel | 4130 | None | 86L20 | |
Alloy Steel | 4140 | Possess | 41L40 | |
Alloy Steel | 4150 | High | ||
Alloy Steel | 4340 | Machinability | ||
Alloy Steel | 4615 | |||
Alloy Steel | 4620 | |||
Alloy Steel | 6150 | |||
Alloy Steel | 8620 | |||
Stainless Steel | 304 | 321 | 303 | |
Stainless Steel | 305 | 347 | 309 | |
Stainless Steel | 316 | 410 | 310 | |
Stainless Steel | 384 | 443 | 416 | |
Stainless Steel | 431 | 420 | ||
Stainless Steel | 430 | 430F | ||
Stainless Steel | 440A,B,C | 440F | ||
Copper Alloys | 110 | 316 | 360 | |
Copper Alloys | 260 | 353 | 385 | |
Copper Alloys | 510 | 356 | 485 | |
Copper Alloys | 651 | 544 | ||
Aluminum Alloys | 1100 | 2017 | 2011 | |
Aluminum Alloys | 2014 | 2024 | 7075 | |
Aluminum Alloys | 3003 | 6061 |
Thread Depth and Starts
Depth of thread is dictated by the amount of load and individual thread strength required. A standard series of diameter-pitch combinations for Acme threads in most cases work well and can be used to start the design. Other popular, though not standard, series for worm threads also work well. Cold forming dictates a maximum depth/ diameter ratio, d/ D, depending on flank angle. The maximum ratio should not be specified if a shorter tooth depth will suffice. It is important not to exceed a maximum ratio because the root area of a thread being forged must be of sufficient size to withstand the forging pressure. If the ratio is too high, the work piece will either fracture at the thread base or try to extrude down the thread axis, rather than roll form transverse to the thread axis. A good place to start a design is to let lead equal pitch (L = p) and thread depth equal half the pitch (d = 1/2 p). For good rolling lead angles should be limited to 6° per start. Lead angles of 1° – 5° per start are typical.
If maximum thread depth is exceeded, then a multiple start thread should be considered. For a two start thread, for example, let lead equal twice the pitch (L = 2p). Again, let thread depth equal one-half the pitch, and check the table to see if the recommended maximum ratio is exceeded. If the thread is still too deep, then 3, 4, 5, or more starts may be needed. (A start is a continuous thread on a shaft; pitch is the distance from one crest, or root, to the next, regardless of number of starts.)
Table 36
ARow | BLead Angle, λ (°) | CNumber of Starts | DPreferred Flank Angle,φn (°) | EMinumum Flank Angle,φn (°) | FMax Depth-to Diam Ratio |
---|---|---|---|---|---|
0 to 10 | 1 - 2 | 14.5 | 14.5 | .167 | |
10 to 20 | 2 - 4 | 20 | 14.5 | .200 | |
20 to 30 | 4 - 6 | 25 | 20 | .250 | |
30 to 40 | 6 and up | 30 | 25 | .250 |
Thread Crest and Root
During thread rolling, material flows around the die in a manner similar to fluid flow around an airplane wing or boat hull. Broken surfaces and sharp corners should be avoided because they interrupt material flow and cause turbulence. Poor thread crest and root design will result in poor surface finish and short die life. Good design has a relieved root, generous crest, and root corner radii. These permit low die penetration force and smooth, eddy-free material flow. Also, strength, finish, and appearance are greatly enhanced.
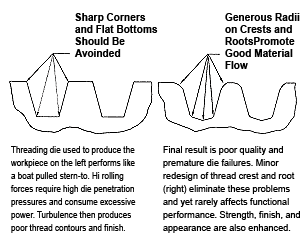
Figure 7
Part Configuration
Because thread rolling is a chip-less process, starting stock size approximates the finished pitch diameter. This contrasts with thread cutting techniques, which require a starting stock size equal to the major diameter. Also, thread rolling tools are much larger than thread cutting tools, so parts must be designed for greater tool clearances. Naturally, designers in the habit of working with cut threads will have to look out for these problems.
Avoid end journals the same size or larger than the thread minor diameter. They will not allow parts to be thread rolled unless an expensive stepped blank is made. A better design keeps all journals smaller than the minor thread diameter. These journals can be turned before or after threading (see Figure 8).
To provide enough strength in the roll die, die width must be larger than work piece width. Usually, the die is 2 to 3 pitches wider for single start threads and 3 to 6 pitches wider for multiple threads. To avoid interference with the die and resultant die breakage, the work-piece must have adequate clearance. Because this clearance is not necessary on hobbed or milled worms, the change to a rolled worm often requires the redesign of areas adjacent to threads. Square ends are impossible to roll onto a work piece. If they are critical, a tapered edge can be ground off. Alternatively, threads can be rolled on long bars, then drilled and cut off in a screw machine (see Figure 9).
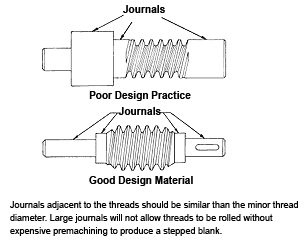
Figure 8
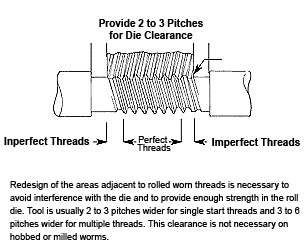
Figure 9
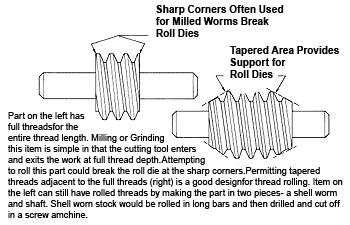
Figure 10
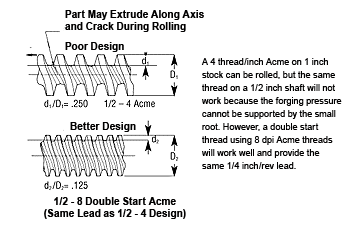
Figure 11